Overview
A glass fabrication company approached us with a slew of problems they were looking to solve - preventable downtime issues on major production lines due to electrical cabinet overheating, worn-out gaskets, rusted bearings, broken camshafts, flooded motors and more.
They were looking for a system that could catch when major inputs into the factory were having elemental problems, like water, air, and power and alert them in real-time to stop production and fix the issue, before things started breaking down.
Approach
Immediately we knew certain things had to be implemented: water detection, vibration, and current sensors in all mission-critical assets.
- We came out to their facility and analyzed all key flows, how product moves through different departments and where natural bottlenecks accelerated unplanned downtime losses.
- Together with their maintenance team, we looked at how running production 24/7 affects certain machines and makes preventative maintenance more difficult.
- After sitting down with administrative staff and drafting a plan to protect and analyze critical machines, or Tier 1 (from our fiscal analysis), like their cutting, polishing, and heating lines, we set out to source the best sensors for their particular facility.
Work Line
Implementing the solution after the arrival of materials took a single day. We outfitted the water filtration system that supplies the entire factory with clean water, with water detection sensors along key pipes and at the base of pumps that send it into machines to make sure before machinery is affected, alerts can be sent via call to technicians on station to shut off the water supply.
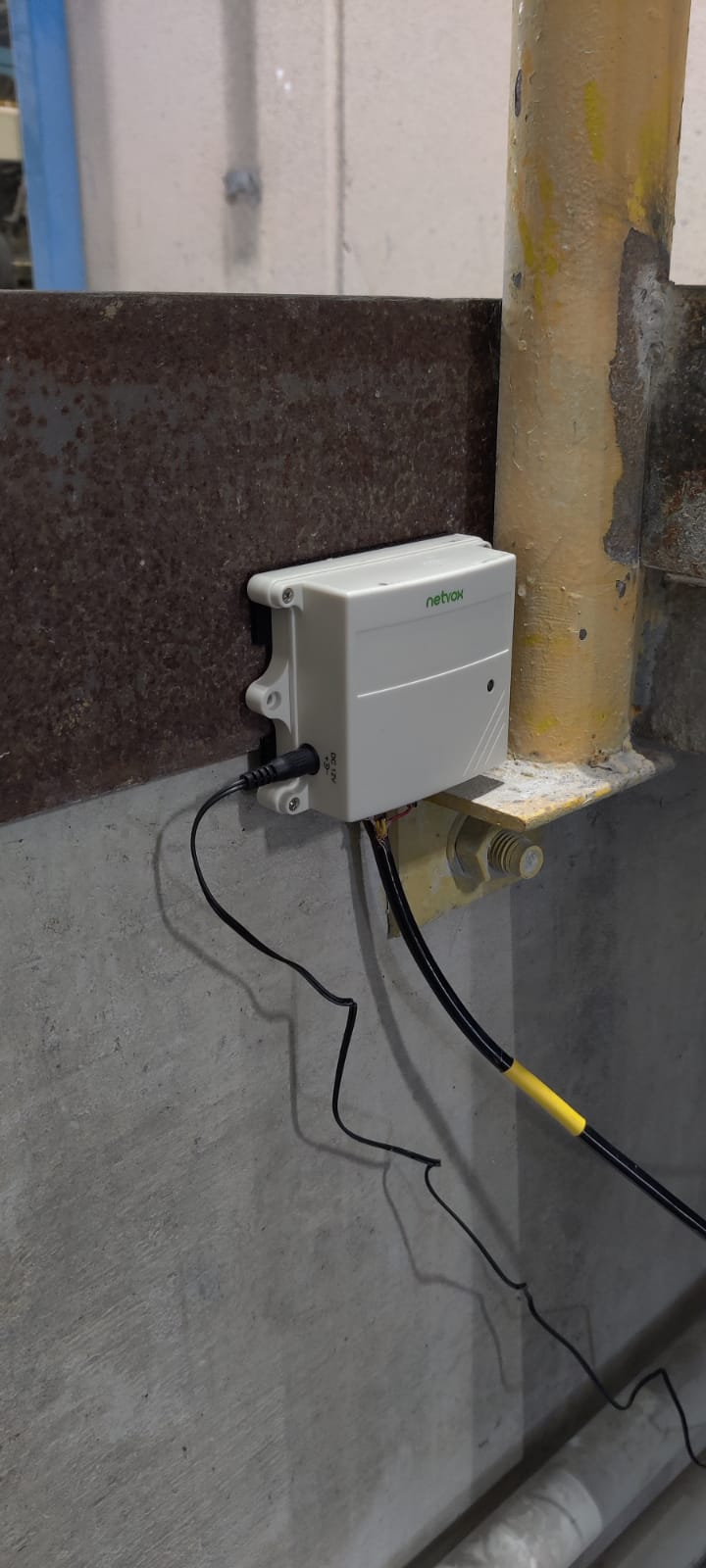
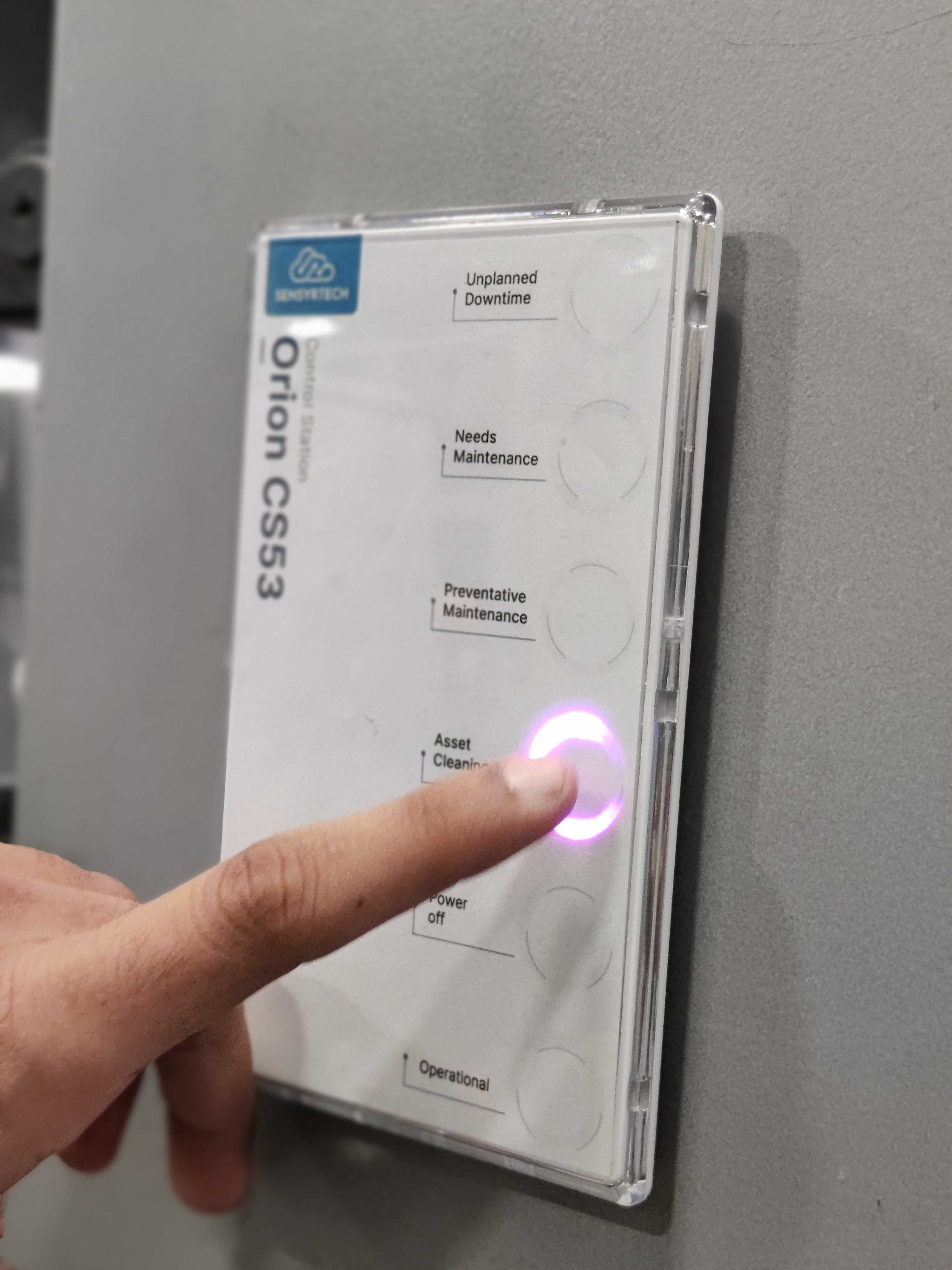
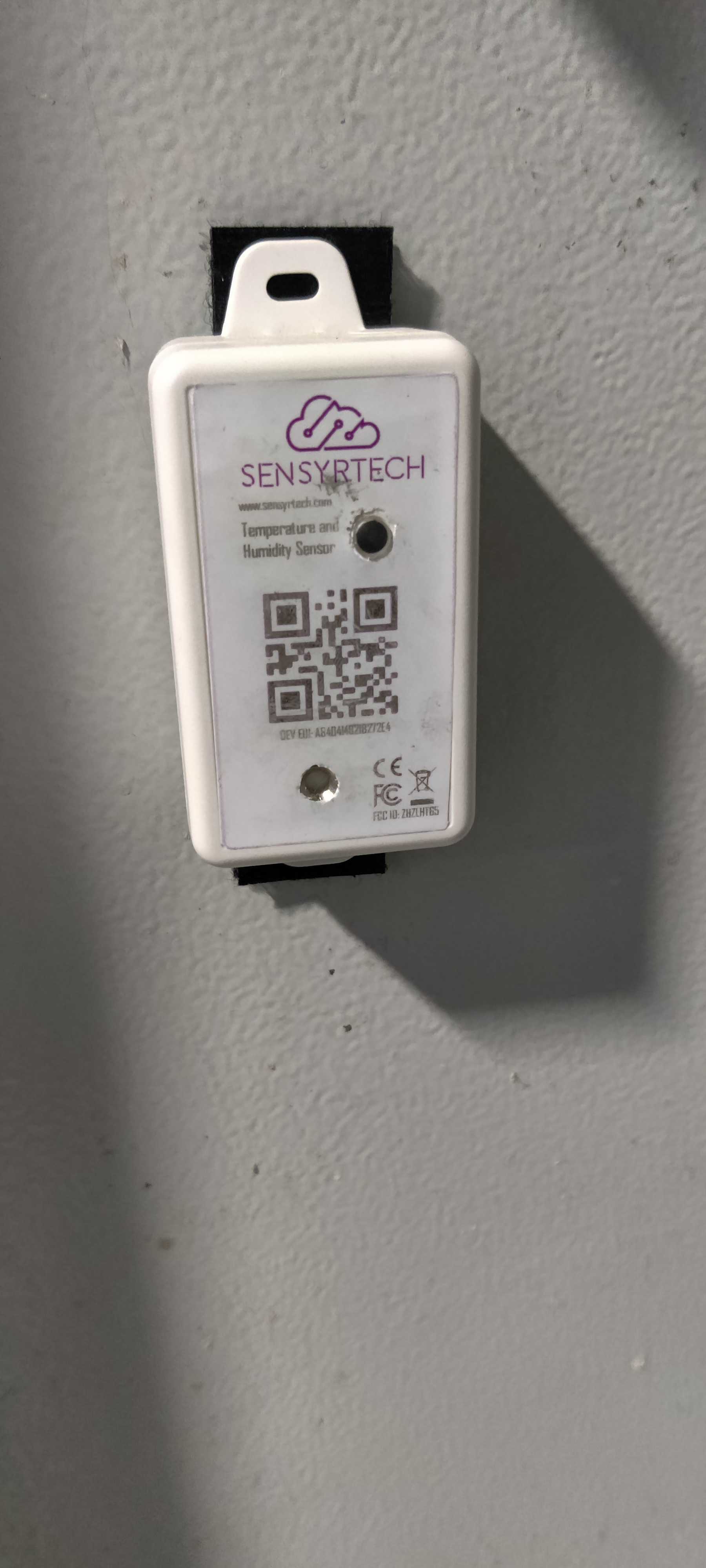
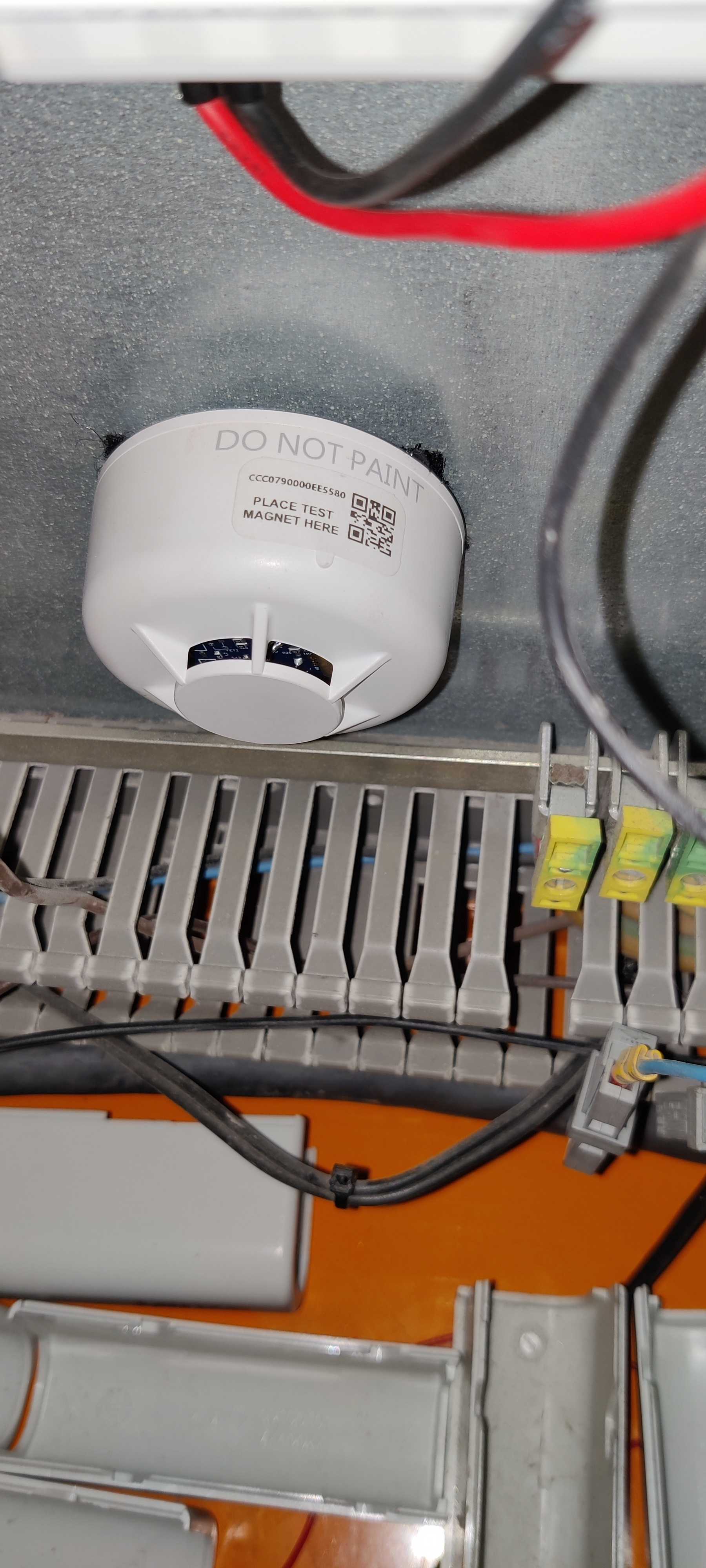
Testing and scaling impact
Current/Amperage donuts and larger 3-Phase power monitors were retrofitted onto key electrical wires on their largest industrial motors to analyze machine health and see how spikes in power were affecting the furnace. Proximity sensors were attached to containers, so porters could be automatically notified to remove waste and raw materials, so production never had to stop.
- Our team understood that not all problems could be caught by sensors, and certain things would inevitably require operator intervention.
- To ease the communication and share responsibility on post-mortems, we helped install multiple Orion CS53 Control Station at each station, so operators could signal Downtime, Attention Required, Standby, or other Asset States on machines.
- These states were configured to automatically call technicians, update statuses in the application so sales personnel could know that critical downtime was affecting production and accordingly shift estimates.
-
Impact
Boosted efficiency and better insight
- Technicians are called or messaged on their phones automatically by Sensyrtech systems, and check into maintenance assignments by acknowledging via SMS.
- Once they complete their tasks, they can update statuses and complete postmortem logs in the clean and simple incident report that is automatically generated.
-
- This helps create a database of incidents and their resolutions, allowing problems to be rapidly diagnosed and fixed.